There are many tools which can be used to assess the environmental impact made by your company and to find opportunities for improvement. Use the tools to improve your understanding of the impacts being made by your company, the opportunities available and how measures can be used to differentiate yourselves from your competitors.
Fault Tree Analysis
There are many ways to assess how a product can fail, 2 are shown below which will help to identify weaknesses in the product design and allow action to be taken to mitigate product failure risks. Product reliability improves competitiveness and improves customer satisfaction (Stamatis 1947). A fault tree analysis is a systematic approach to identify potential root-causes for product failures. A fault tree analysis is a top-down structured logic diagram to systematically determine where and how a failure might occur as shown in the diagram below. Fish bone or Ishikawa diagrams can be used to assist the process to understand the potential fault areas.
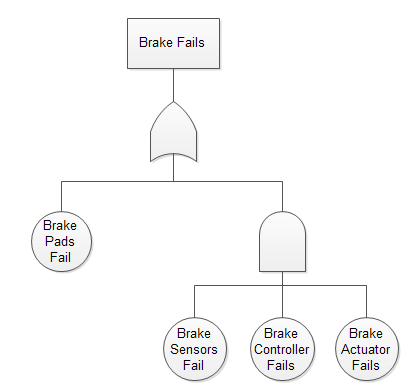
Environmental Risk Assessment
ERA is an examination of the risks from a product that threaten ecosystems, animals and humans. The approach can be quantitative or qualitative and can include health risk assessments and ecological risk assessments. The steps to undertake an ERA are:
- Hazard identification – looks at the potential hazards that could affect humans or the environment. These hazards could be from the product or by-products during the product lifetime or at end of life disposal
- Effects assessment – studies the levels by which the chemicals used would start to have an effect to humans or the ecosystem.
- Exposure assessment – looks at the Predicted Exposure Concentration, or total daily intake of humans or the ecosystem.
Lifecycle Assessment
LCA aims at specifying the environmental consequences of products or services from cradle-to-grave. The assessment considers all environmental impacts of the product or service from the raw material extraction, production, distribution, use, maintenance, remanufacture, recycling and disposal. LCA allows problematic areas within the supply chain to be identified, alternatives considered and the most appropriate option to be chosen.
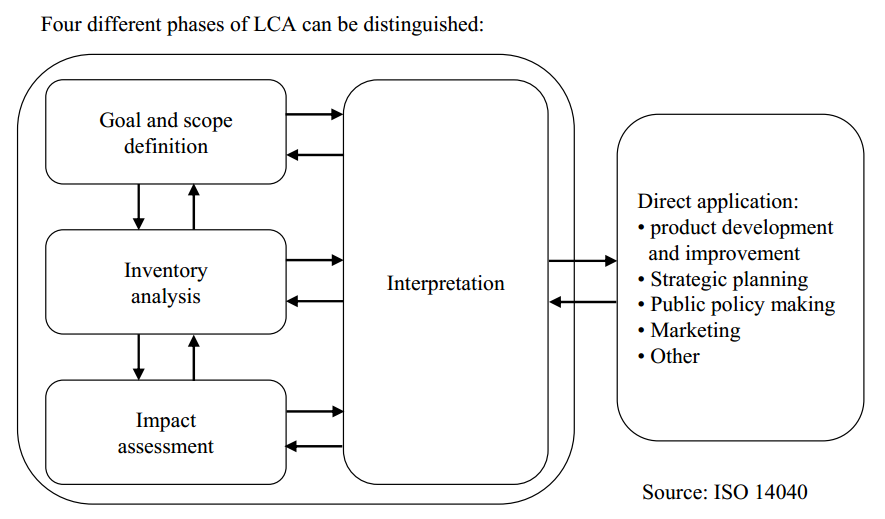
- Goal and scope definition – define what the boundaries of the analysis will be.
- Inventory analysis – data collected from the business, literature and software to determine the impact through the life cycles.
- Impact assessment - emissions (either solid, liquid or gaseous) are categorised. Each category is then characterised to determine the magnitude of the environmental impact and a value is placed on each emission.
- Interpretation – use the figures to calculate areas of greatest potential improvement.
- Direct application - implement the changes according to the life cycle assessment.
Material Flow Analysis
Material flow analysis considers the pathway of materials in, out and through the business and how they are acquired through virgin or waste-recovered sources. This can allow better understanding of the causes and effects to environmental issues, such as material flows to landfill, the environment or through recycling loops (Wrisberg and Haes, 2002). An example of a material flow analysis is shown below in a Sankey diagram:
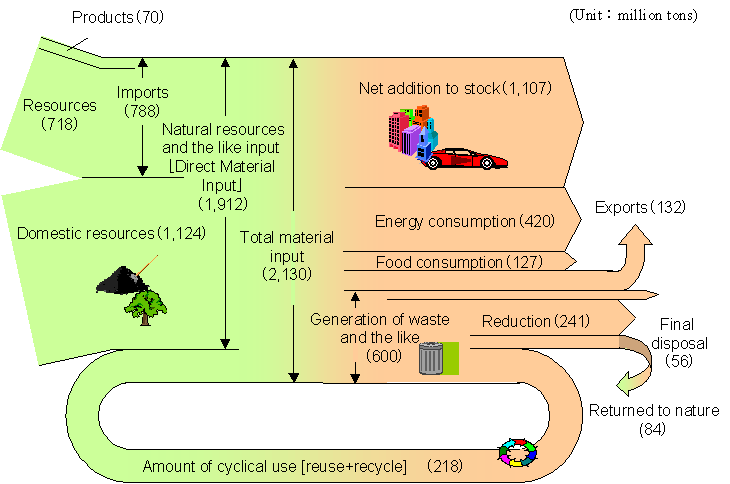
Life Cycle Costing
Life Cycle Costing analyses the costs incurred by the product across its lifespan including manufacture, usage and disposal. These can include the direct costs to the customer, such as original purchase cost, energy costs, maintenance costs etc. LCC also puts a monetary value on emissions, resource and environmental and human health effects considered in the Environmental Risk Assessment. (Wrisberg and Haes, 2002)
Material Input Per Unit of Service
Material Input Per unit of Service (MIPS) is used to measure the eco-efficiency of a product. It is calculated by dividing the material input of all man-moved materials consumed throughout the product life-cycle by the number of service units. Using a car as an example, the MIPS is calculated by adding all materials and energy used to manufacture, distribute, maintain and use the car, then dividing by the total number of passenger kilometres completed across the car’s lifetime. (Wrisberg and Haes, 2002)
Cumulative Energy Requirements Analysis
The Cumulative Energy Requirements Analysis (CERA) states the entire demand valued as primary energy for production, usage and disposal. The CERA is stated in terms of joules for energy consumed. However, the calculation can then be converted in to analysis such as emissions throughout the product lifecycles. The calculation for CERA is the sum of the energy requirements for production, use and disposal.
Failure Mode and Effects Analysis
Failure Modes and Effects Analysis is another systematic approach for failure analysis for a product or process. Design for FMEA considers each part of the product and analyses:
- Potential failures that could occur
- State of operation at the time, e.g. moving, standby, loaded etc.
- Effect of failure to the component and system
- End effect of failure
- Probability of occurrence
- Severity of failure
- How the failure will be detected
- Risk Level (through multiplying score of probability, severity and detection)
- Mitigation action to reduce the risk level of the failure
Cost Benefit Analysis
Cost benefit analysis is used to determine whether the benefits of an investment or design change outweigh the costs. The analysis expresses all positive and negative effects of an activity to monetary value. Although the analysis easily shows the cost and benefits with a single indicator it can be difficult to quantify and value the environmental benefits of a proposed change. (Wrisberg and Haes, 2002)
Further Tools
To see more decision support tools, the Institute for Manufacturing at the University of Cambridge have consolidated over 70 tools here.